Overview
CiDRA Concrete Systems has developed the SMARThatch™ System featuring AIRtrac technology for real-time information from batch plant to job site. CiDRA partnered with both HED and Exosite to develop a connected solution that helps their customers leverage real-time data to enhance concrete quality, optimize processes, and reduce costs.
The Opportunity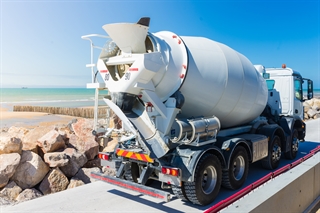
Concrete is one of the most widely used matrials in the world and is a constant presence in our daily lives. From parking garages and bridges to roads and buildings, concrete forms the infrastructure and foundation for much of our commercial, residential and transportation structures.Given its many critical uses, the quality of the concrete is of the utmost importance.
In order to achieve optimal strength and long-term durability, the perfect combination of aggregate, cement, water, and air must be created for each application. CiDRA Concrete Systems understands the challenges involved with producing concrete and is why they developed the SMARThatch™ system, which features AIRtrac™ technology, giving their customers the ability to monitor the entrained air content in real-time while being transported from batch plant to job site.
Other methods used to monitor air content involve a highly manual process that requires on-site technicians to complete. Testing can only be completed once a truck arrives on the job site, resulting in costly downtime if air content adjustments are required. Test results only provide insight into the quality of a single sample, rather than the entire load, and give no indication about when or how changes in quality may have occurred.
To optimize their operations, concrete producers and truck operators need greater visibility into these key metrics throughout the mixing process in order to identify issues earlier, adjust loads proactively, and provide real-time feedback about concrete quality to the plant.
The Solution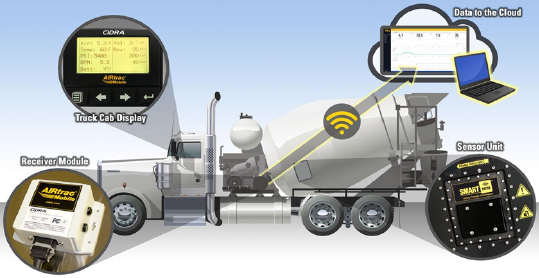
CiDRA partnered with HED and Exosite to develop their SMARThatch monitoring system, which is installed on the mixing drum of concrete trucks. As the drum rotates to agitate the concrete, the sensor unit collects data on air content, temperature, drum rotation speed, and volume.
Sensor data is sent to the HED CANect® Telematics unit, along with an in-cab display for truck operators that provides real-time air content and temperature data that they can access during transit from the batch plant to the job site. The Telematics unit then transmits the sensor data, along with GPS and other key metrics, over the 4G LTE cellular interface to the back office for visualization by remote users. In addition to the collection/transmission functionality, over-the-air reprogramming enables field-based software updates into the future.
The HED Telematics back office utilizes Exosite’s platform, where data is aggregated and visualized using the ExoSense® condition monitoring application. From this tool, business owners, quality control personnel and truck operators can view truck-specific dashboards with real-time and historical information that can be used to identify batch issues, enhance quality control coverage, and test new mix designs. Users can also export historical data, receive notifications, see fleet-wide data views, leverage hierarchies to manage customers, and more.
The Results
For CiDRA Concrete Systems:
• Provided speedy deployment
○ By partnering with both HED and Exosite, CiDRA Concrete was able to leverage a pre-integrated hardware and software solution that streamlined their path to the cloud. Rather than struggling with connectivity, they quickly had a fully functioning proof of concept to test with customers, allowing them to focus on marketing and business development for their new product.
• Enabled new recurring revenue stream
○ CiDRA Concrete transformed itself from a traditional product development company into a software-as-a-service (SaaS) company. Rather than a one-time, hardware-based sale every few years, CiDRA Concrete now benefits from recurring software subscription fees.
For CiDRA’s customers:
• Reduces downtime and waste
○ Access to real-time air content and temperature data helps operators catch issues early, so they can make adjustments to loads prior to arriving on a job site. Key personnel can also be notified so that subsequent batches are modified to remain within specification.
• Lowers costs and variability
○ With less manual testing, operators save valuable time and additional costs. Also, by continuously monitoring the entire load, rather than random samples, operators experience more accurate test results and less variability.
• Enhances quality control
○ Continuous monitoring provides insight about precisely when, and under what conditions, air content began to change. This can be compared with changes in the production process that may have triggered air content changes. When extended over multiple projects and multiple concrete mixtures, this becomes a powerful tool to help producers enhance quality and consistency.